Lessons Learnt: "Beer Cans" for Rocket Fuel Sloshing | Jupiter Missile
Learn why the US Air Force used "Beer Cans" in the second Jupiter Missile test. The answer lies within the problem of rocket fuel sloshing.
Rocket science is involved. There is a lot of technical nitty-gritty to be understood. Over the years, a lot of new science, mathematics, and technologies have emerged from Space Programs. Like we learned the stability characteristics of a rotating rigid body which is losing kinetic energy through internal forces in the previous Lessons Learnt article. But learnings from the Space Programs of the world are not limited to science and technology. Aerospace engineering, a highly interdisciplinary field, requires top-level project and human management skills as well. Today's story, from NASA's archives, introduces us to 'Baffles' a device used in liquid propellant engines while making us recognise the importance of Human Creativity. The story starts in the year 1957 when NASA began testing the Jupiter Missiles. The later variants of the same Jupiter missiles launched Pioneer 4, the first successful American lunar probe.
Jupiter Missile
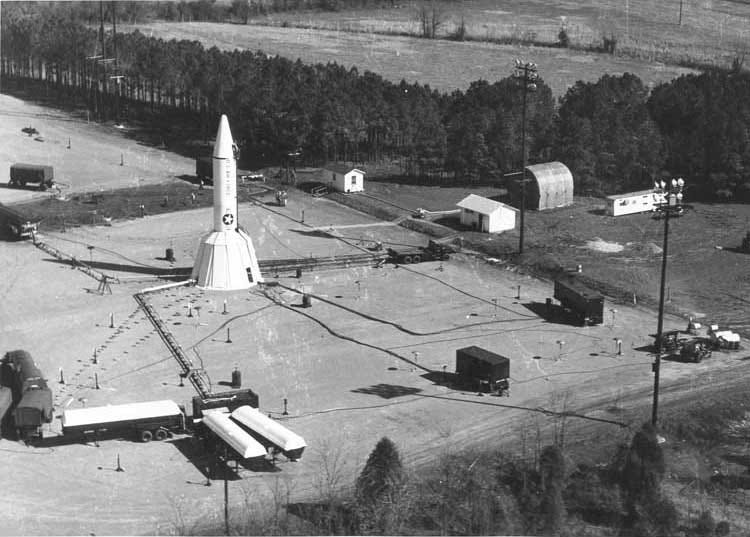
The Jupiter was the First nuclear-tipped, medium-range ballistic missile (MRBM) of the United States Air Force (USAF). It used RP-1 and LOX as liquid fuel for the single Rocketdyne LR79-NA (model S-3D) rocket engine.
The Jupiter missile might be overlooked today, but without it, there would have been no Army Ballistic Missile Agency (ABMA), no Explorer I, no Saturn launch vehicle, and no Marshall Space Flight Center. Without Jupiter, U.S. astronauts would not have walked on the Moon in 1969.
Ed Kyle, Space Launch Report
Problem
On March 1st 1957, the first Jupiter missile AM-1A was launched from the Launch Complex-5 at Cape Canaveral. The vehicle broke up at T+73 seconds after control failed around the 50 seconds mark. The second Jupiter Launch, on April 26th, went as planned until T+70 seconds. The rocket then broke up at T+93 seconds due to instabilities related to Propellant Sloshing. The first problem was attributed to the burning of control wiring by turbopump exhaust. Therefore extra insulation was added in all subsequent flights. Though, the second problem, related to Propellant sloshing dynamics coupling with the control system was not easy to solve. Hence required more creativity.
Physics
We all have experience liquid sloshing in our lives. We have spilt liquids such as water, tea, coffee and juices when trying to go fast while a filled cup. What happens is that the liquid starts resonating with our movements, and it makes the control of the cup difficult. We tend to slow down to stop this sloshing or put a lid over the container.
Similarly, rockets filled with liquid propellants also experience this sloshing. While we have the option of slowing down and stop the sloshing rockets can't reduce their speeds. And even with closed containers, the problem is not spilling but causing instabilities to both combustion and control. Therefore, it is essential to understand this slosh dynamics. There are many good books on slosh dynamics which tackle this through an analytical point of view. But this theory is reasonably recent and did not exist in the year 1957.
Solution
While NASA had a team studying slosh dynamics using both analytical and experimental techniques, Jupiter 3 had to be launched within a month. The engineers took the Jupiter LOX tank, filled it with water and put it on an empty railroad car. Using a movie camera, they recorded the motion of water when the railroad car bumped against the spur railroad stop. They derived an equivalent slosh mass and frequency to be used in a control feedback simulation. This creative empirical technique would now help them test their control systems with a better environment.
But this was not the solution to the sloshing problem. As the phenomenon was still not well understood, the sloshing could be very different for the launch. It was at this point that human experience and creativity combined to help design a new device. An engineer remembered something from when he was back in farms. To haul water in steel drums in a wagon, he floated pieces of lumber on the surface to keep it from spilling. But a missile cannot of lumber floating in its fuel tanks! Therefore they designed a perforated cylinder truncated with cones and had a commode float inside to make it float. These new devices were called "Beer Cans". The whole fuel tank surface was covered with these devices, and Jupiter 3 was successful.
Later, through analysis and sub-scale testing, "Baffles" were developed. These were structures included in all subsequent liquid engines to prevent sloshing of liquid. The following link has information about the F-1 engine Baffles.
"The basic lesson is that we must reward all forms of creative actions of our people and start development of processes to remove inhibitors which suppress the creative actions of its people."
NASA Report